The production speeds for laser cutting machines can vary depending on several factors, including the type of material being cut, the thickness of the material, the complexity of the design, and the power of the laser.
Here are some general guidelines for production speeds for laser cutting machines:
Material type: Different materials have different production speeds for laser cutting. For example, metals such as steel and aluminum generally cut faster than materials like wood, acrylic, or foam.
Material thickness: The thickness of the material being cut affects the production speed of the laser cutting machine. Generally, thinner materials can be cut at higher speeds than thicker materials.
Laser power: The power of the laser is a key factor in determining the production speed. Higher laser power generally allows for faster cutting speeds, although this can also depend on the other factors mentioned.
Design complexity: More complex designs and shapes will generally take longer to cut than simpler designs, as the laser must follow a more intricate path.
Machine configuration: The configuration of the laser cutting machine, including the type of laser and the cutting head, can also impact production speeds.
Overall, production speeds for laser cutting machines can range from a few inches per minute up to several hundred inches per minute, China Co2 Laser cutting machine depending on the specific factors involved. It’s important to work with an experienced laser cutting service provider to determine the best production speed for your specific application and to optimize the design for maximum efficiency.
How can I optimize my design for maximum efficiency?
Optimizing your design for maximum efficiency in laser cutting involves several factors that need to be taken into consideration. Here are some steps that you can follow:
Material selection: The first step is to select the most appropriate material for your design. Different materials have different cutting properties, and selecting the right material can help to improve cutting efficiency.
Material thickness: The thickness of the material being cut affects the production speed of the laser cutting machine. Generally, thinner materials can be cut at higher speeds than thicker materials. If possible, consider using thinner materials to improve efficiency.
Design simplicity: More complex designs and shapes will generally take longer to cut than simpler designs, as the laser must follow a more intricate path. Simplifying your design can help to improve cutting efficiency.
Nesting: Nesting is the process of arranging multiple parts on a single sheet of material to maximize material usage and reduce waste. Proper nesting can help to improve cutting efficiency by reducing the number of cuts required and minimizing material waste.
Cutting path optimization: The path that the laser takes when cutting your design can impact cutting efficiency. Optimizing the cutting path can help to minimize the distance that the laser must travel, reducing cutting time and improving efficiency.
CAD design optimization: Optimizing your CAD design can also help to improve cutting efficiency. Consider using fillets instead of sharp corners, and avoid overlapping lines or open contours, which can increase cutting time.
Overall, optimizing your design for maximum efficiency in laser cutting requires careful consideration of several factors. It’s important to work with an experienced laser cutting service provider who can provide guidance on material selection, nesting, and cutting path optimization, and who can help you optimize your CAD design for maximum efficiency.
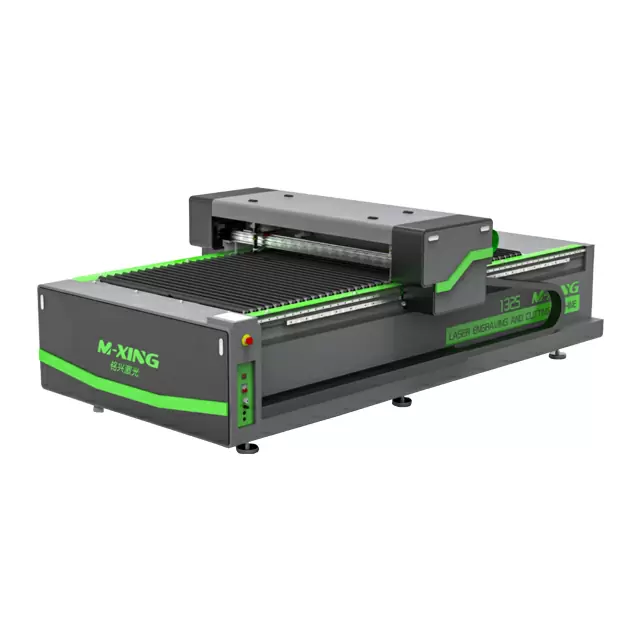